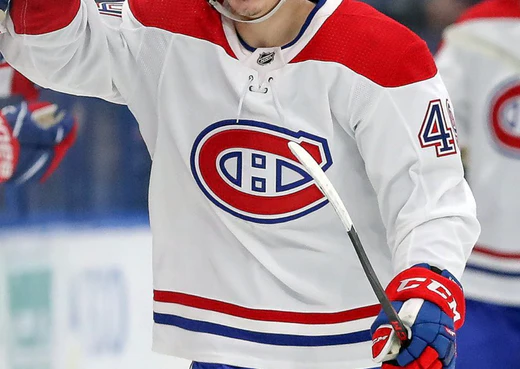
- Through its local production, SP Clothing reduces transport between the various stages of production, which means fewer GHG emissions.
- Its threads used to weave their fabrics are composed of 100% recycled polyester
- In 2021, this factory set up a green committee!
If we had to identify the greatest strength of SP APPAREL,
, a sports uniform manufacturer since 1999, it would undoubtedly be its impressive autonomy. The manufacturer, which notably crafts all the socks and jerseys for the 32 NHL teams, operates an almost fully integrated production chain. From knitting their jerseys to cutting their patterns and producing the finished product, it all happens in their brand-new factory in Saint-Hyacinthe.
This predominantly local manufacturing not only creates jobs but also comes with a host of eco-responsible benefits. Less transportation between different production stages means fewer greenhouse gas emissions. This full control has also allowed them to make a significant shift in the past year— the threads used to weave their fabrics are now made of 100% recycled polyester.
The origin of this initiative? The happy marriage between the owner, Steve Bérard's desire to make his activities more environmentally friendly and the growing demands from clients like Nike for eco-designed goods. This change in direction is particularly noteworthy considering SP Clothing's production capacity, which can reach up to one million units per year.
The desire to do better was also felt among the employees with the creation of a green committee in 2021. Comprising representatives from different departments, from the factory to the administration, the group can address a range of concerns that may be less obvious to others but have real impacts. Currently under study? The recovery of paper used in sublimation (a printing technique) and the elimination of plastic in their delivery boxes.
Finding outlets for textile scraps, inevitable in the cutting of the approximately 50 pieces that make up each jersey, is also on their radar. Could their waste become the raw material for another product? Like many players in the industry, shredding them to make filling seems to be the most promising avenue, but finding a buyer is still necessary.
In the coming years, it is hoped that this question, on everyone's mind, will be answered.
The distribution of this article is made possible by the contribution of Détail Québec, the retail sectoral workforce committee.